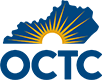
Workforce Training Case Studies
It started as a simple idea. Could manufacturers resolve skilled technician shortages by tapping into a valuable resource that many had within their own facility – female production workers? A collaboration of industry, workforce, and educational partners in Owensboro, Kentucky pursued this idea which led to the design and launch of the GO Females program.
GO Females is an acronym for Greater Owensboro Facilitating Equitable Manufacturing and Leadership Educational Solutions. The purpose is to "skill up" underserved incumbent workers in manufacturing for both technician and leadership positions. With support from the National Science Foundation and the Kentucky Workforce Development Cabinet, Owensboro Community and Technical College (OCTC) launched its first GO Females cohort in 2019.
GO Females is an industrial maintenance associate’s degree program offered in a hybrid format at or near the worksite. It targets those currently working in manufacturing who need to continue working full-time while taking classes. The GO Females delivery model includes instructor-led teaching combined with competency-based online learning offered through the industry-validated Advanced Manufacturing Technical Education Collaborative, known as AMTEC.
The first GO Females cohort of students was comprised of 20 female workers from UniFirst Corporation in Owensboro, Kentucky. UniFirst Corporation employs 445 individuals at its state-of-the-art Owensboro Distribution Center that provides customized work uniform programs, corporate attire, and facility service products. UniFirst supported GO Females students by paying participants full-time wages and benefits throughout the program and providing them eight hours of paid time off per week to attend classes. Fifteen students graduated with an associate’s degree in 2021.
The partnership with AMTEC allows OCTC’s GO Females program to provide working females unprecedented access to education by eliminating accessibility barriers. As a true “work and learn" model, it brings college to the workplace. Classes are held onsite and lab training equipment is set up near UniFirst’s actual production equipment. This allows instructors to connect the AMTEC concepts students learn to “real world” application. It also allows the students to understand, practice, and apply skills relevant to what occurs on the job.
At Unifirst, GO Female students overcame the challenges of balancing coursework with a full-time work schedule (often 50+ hours a week) and the impact of COVID, to graduate in 2021. Out of the 20 original GO Females students, 15 completed the program in July 2021 with 66 credits.
These 15 students earned an Industrial Maintenance Technology Associate in Applied Science Degree, along with a diploma and several certificates. GO Females students earned a 3.57% average GPA and filled critical industrial maintenance jobs at the plant.
Case Study - Documenting Standard Operating Procedures
Glenmore Distillery, a division of Sazerac, boasts one of the largest and most modern bottling facilities in the country and continues to be a sizable employer and fixture in the city Owensboro, KY. Like many companies, they are facing many retirements in the coming years. Those retirees will leave with expert knowledge of the operations of their bottling facility. That knowledge, gained over many years could be lost if not captured. This is a time-consuming task for both the human resource personnel and the employees that run the bottling lines at Glenmore. Therefore, Glenmore contracted with Workforce Solutions to capture the standard operating procedures, troubleshooting and maintenance of one of their 50ml lines.
With the help of veteran employees that run the line, Workforce Solutions created a manual that detailed every action necessary to start the line, run the line, change the product labels, correct runtime faults, shut down the line, report necessary data and maintain a safe and orderly area. They documented each minute task with both outlines and pictures of the actual equipment on the line. Several employees who were experienced with the line reviewed the manual multiple times, offering suggestions and revisions.
In the end, new-hires will have a detailed manual to assist them that includes all of the different “work-arounds” that have been discovered over the years!
Case Study - WAUPACA FOUNDRY
Tell City, Indiana
At OCTC’s Hancock County Center, Workforce Solutions recently completed a series of employee skill assessments in a variety of disciplines for Waupaca Foundry. Phase One of the assessment process utilized computer-based training followed by a quiz to assess skill levels. In Phase Two, hands-on assessments were conducted in the equipment lab.
Assessments areas included:
- Measurement
- Welding
- Rigging and Lifting
- Blueprint Reading
- Hydraulics
- Pneumatics
- Pipe Fitting
- Fasteners
- Machine Layout
- Power Train, which included Chain and V-belt Drives.
Waupaca managers use the results of these assessments to determine and plan employee training needs.
CASE STUDY:
GO FAME – When Community Partners Address Critical Workforce Shortages
Across the nation, manufacturing is undergoing a resurgence critical to the economy. Production and the related jobs lost to overseas competition are being regained thanks to the high caliber of goods produced by American industry. Unfortunately, this resurgence and accompanying prosperity are threatened by an escalating shortage of skilled manufacturing technicians necessary to meet both growing industry demands and the job openings created by the increasing number of retirements of skilled workers.
While many communities are grappling with the challenges surrounding this issue, partners in this region have built upon years of successful collaboration to initiate a new, industry-driven, work and learn model as a key strategy in this community’s workforce development tool kit. The program, known as Greater Owensboro Federation of Advanced Manufacturing Education or “GO FAME”, is based on a model established at Toyota North America and the Kentucky Community and Technical College System. The FAME model enrolls a select cohort of students in an Advanced Manufacturing Technician (AMT) or Computerized Manufacturing Technician (CMT) degree program delivered by Owensboro Community and Technical College while concurrently placing them in a technician oriented position at a sponsoring manufacturing employer. Participating students must be high school graduates and willing to learn and work in an accelerated, eighteen-month, multi-craft manufacturing technician program. Program students are full-time participants, attending class two full days per week and working as paid employees of their sponsoring company a minimum of three days per week.
The GO FAME chapter, along with its inaugural student cohort of fifteen students, was launched in a whirlwind timeframe. In little more than three months, partners created a 501 C3 followed by intensive recruitment efforts to select applicants interested in pursuing highly-competitive and well-paying, manufacturing careers. To date, 22 companies, in partnership with the Greater Owensboro Economic Development Corporation and Owensboro Community and Technical College, have joined the Kentucky FAME movement launched in 2014 by Governor Beshear. OMICO Plastics, Inc., Kimberly Clark, Metalsa, Toyotetsu Mid America, Castlen Steel, Sun Windows, Precision Roll Grinders, Inc., Domtar, Trifecta Steel, The Hines Group, Inc., Ken-Tron Mfg., Inc., UniFirst, Hunter Douglas, National Office Furniture, Specialty Food Groups Inc., Big Rivers, Daicel Safety Systems America, Perdue Farms, Miles Enterprises, Hollison Technologies, ADM Industries, and Yager Materials are standing members of the greater Owensboro chapter.
The synergy, excitement, and preliminary success experienced to date demonstrates the tremendous relevance of the program model to industry, education, workforce, andeconomic development stakeholders. GO FAME’s unique employer/educational model provides greater relevance and mastery for the student learner since classroom skills are reinforced in the workplace setting. Company partners benefit by “growing” a technician who understands not only its unique production processes but also its overall culture and business practice. Of particular note to families with college age students, as well as individuals interested in career advancement, GO FAME provides an excellent college education and well-paid job options upon graduation. The AMT degree transfers into numerous 2 + 2 options at the University of Kentucky, University of Louisville, Western Kentucky University, and other four year industrial management and engineering-related postsecondary degree programs. Since students earn wages for time spent on their job and sponsoring companies assist with tuition costs, the AMT degree is earned with little or no college debt.
The GO FAME Chapter is committed to developing new program options to address other skilled workforce technician shortages in manufacturing, as well as supporting the Work and Learn model’s applicability to other industry sectors. In 2017, GO CAREERS, was established with three of the community’s largest employers. The GO CAREERS affiliates will provide a workforce development learning platform for non-manufacturing, related program options. Sun Windows and US Bank are participating in work-based postsecondary credentialing options, such as Leadership Development,Supervisory Management, Business Administration, Finance, Information Technology,while Owensboro Health participates inHealthcare Administration and Office Management.
Student Success Stories
GO FAME was created precisely for students like Chase Smith. As a high school senior from a low-income family with a low GPA, Smith says college didn’t seem like much of a possibility. That is until his career readiness counselor walked up to him one day in Apollo’s cafeteria. “Mr. (Jeremy) Camron laid the application down in front of me and said ‘sign this!’” Smith recalled. “This program saved me. If it wasn’t for GO FAME, I don’t know what I’d do. I can’t learn unless I’m doing it. That’s why this is the perfect way for me to learn.”
Sean Dysinger left a well-paying job after nearly 30 years in sales and marketing to pursue his interest in engineering through GO FAME. “I just wanted something different. Something that I could build upon my other skill sets. It’s never too late to invest in yourself,” he explained.
Clint Morris and Tyler Ashton are somewhere in the middle of that bell curve. Both
are hardworking men who are supporting their families and raising kids while still
balancing school and work. “I drop my son off at school and my backpack is laying
right next to his,” Morris said, with a smile that Ashton returned while admitting
that his daughter has now turned the tables on him. “What did you learn at school
today, Daddy?” For these guys, their work weeks now consist of two full days in class,
alternating with three full days at work. “This is hard; I’m in that lab from 12:15
straight till 5:00,” Chase said. Still, he wouldn’t have it any other way.
2018 Update:
Tyler Ashton is now a supervisor at Amazon
Clint Morris is employed by Castlen Steel
Sean Dysinger is employed by Toyotetsu Mid-America
Case Study: OCTC’s Workforce Solutions …a world class, training partner
As the Aleris Training Director, a four-time Toyota facility start-up veteran, proclaimed, “OCTC is the best college…no the best PARTNER, I have ever worked with!”
In 2014, Aleris Corporation announced its plans to invest $350 million to expand its capabilities at its rolling mill in Hancock County, Kentucky. Operating more than 40 production facilities in North America, Europe, and Asia, the privately held, global leader in aluminum rolled products, serves a number of varied industries including aerospace, automotive, defense, building and construction, industrial, rail and trucking. The project investment will equip the company with the capabilities and the technology to serve the North American automotive industry as it shifts to broader aluminum use to make lighter vehicles. The company was awarded an $11 M incentive package from the Kentucky Economic Development Cabinet with $1M earmarked for new hire skills upgrades required by state of the art production processes.
When it came time to select a training partner for the project focused on changing its North America presence, Aleris chose Owensboro Community and Technical College’s Workforce Solutions division. Since summer of 2015, Workforce Solutions has been the preferred supplier for any support and activity required within Aleris’ selection and training of its CALP–related workforce. The breadth and scope of services provided by Workforce Solutions in the initial phase of the CALP expansion– consultation, research and industrial design, assessment, reporting, hands-on skills training, and employee counseling - fall far beyond standard community college training partnerships. The flexible, highly experienced Workforce Solutions team has met every expectation and workforce timeline, providing timely counsel; developing just-in-time solutions; and immediate responses to any and all changes, timeline revisions, and/or labor management related challenges that arise within a project of this magnitude.
Senior members of the Workforce Solutions team work hand-in-glove with Aleris management charged to design and effect an optimal workforce delivery plan for the expansion. During a nine month period, the team has led critical research with its industrial psychometrician to identify the best options to assess the new hires’ mechanical and electrical competencies; developed a company-specific assessment to determine critical thinking and problem solving abilities, along with a computer-based, on-line tutorial for same; subsequently assuming large scale, technical training responsibilities for the newly hired CALP mechanical and electrical skilled technicians.
Within fiscal year 2015-2016, Workforce Solutions will provide Aleris Corporation more than $750,000 in cutting edge, workforce development programs and services.
Workforce Solutions has:
- Designed and implemented more than 23 customized, advanced manufacturing courses encompassing 1,550 hours of training over a 29 week period for skilled CALP maintenance technicians.
- Offered more than 70 assessment sessions (900+ individual assessments) hosted at the Aleris plant site, college, and career center locations to approximately 300 + incumbent workers and applicants from across the region.
- Developed a customized abstract reasoning tutorial for both traditional and computer-based training (CBT) delivery. Some 123 individuals participated in the CBT hosted on the college’s Flex Train instructional platform. In addition to the CBT option, 17 on-site tutorial sessions were held for those interested.
With its critical importance to both the company and region’s economy, OCTC’s Workforce Solutions is proud to have been selected by Aleris Corporation to serve as its value-added training partner for the CALP initiative. The team takes equal pride in its ability to not only serve as an integral partner in the success of the CALP launch, but its ability to meet and exceed the company’s delivery expectations of an external collaborator.
Case Study: Mobile Workforce Training
“This program will save us money in training dollars, decrease claims and legal expenses, and improve the quality of our service. This will also present a better image of GRITS to the public, our insurance providers, health care facilities, KYTC, and the FTA.”
This 12 module customized refresher course was designed in partnership with Green River Intra-county Transit System (G.R.I.T.S.) specifically for their public transit drivers. In excess of 80 drivers, they found themselves spending thousands of dollars for group training sessions. Scheduling trainings had become a difficult and very stressful task.
These online training modules allows drivers to train and test at their convenience. Whether waiting for a pick-up or had a cancelation, these training modules can be completed on their mobile devices within the vehicle. The built-in training completion verification allows for the manager to be notified when training has been completed and ability to print a certificate of completion for their personnel file. Each driver can receive an annual refresher course for as little as $35 per module.
“This program will save us money in training dollars, decrease claims and legal expenses, and improve the quality of our service. This will also present a better image of GRITS to the public, our insurance providers, health care facilities, KYTC, and the FTA.”
- Dan Lanham, Transportation Director AACS/GRITS Transportation
Modules
- Blood borne Pathogen
- Wheelchair Securement
- Passenger Assistance
- Defensive Driving
- Drug & Alcohol
- ADA Guidelines
- Lifts
- Accident and Incidents
- Child Safety Seats & Booster Seats
- Electric Wheelchair, Jazzy, and Scooter securement
- Emergency Procedures
- Pre-Trip Inspection, End of Day Procedures & General Vehicle Knowledge